ISO Standards Training Courses
Comprehensive training on ISO quality management standards and auditing.
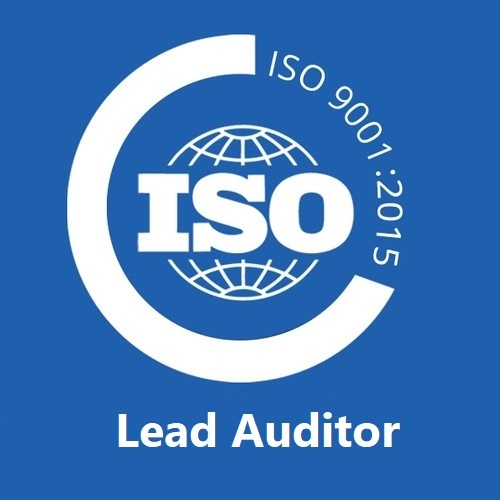
ISO 9001 Quality Management System & Internal Auditor
Learn how to streamline processes and improve operational performance. Develop the ability to conduct effective internal audits and ensure compliance. Align with internationally recognized standards to improve market credibility.
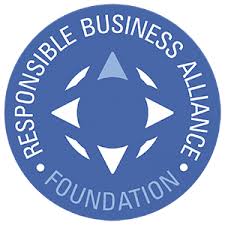
RBA Code of Conduct 8.0
Learn to implement and uphold responsible business conduct. Ensure compliance with labor, health, safety, and environmental standards. Build trust with stakeholders by demonstrating ethical practices. Identify and address risks related to social and environmental responsibility.
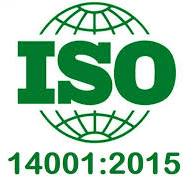
ISO14001 Environmental Management System & Internal Auditor
Equip yourself to reduce environmental impact and promote sustainable practices. Stay ahead of environmental regulations and avoid legal penalties. Learn how to optimize resource use and reduce waste. Gain the skills to conduct environmental audits and drive continuous improvement.
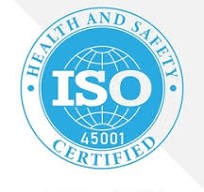
ISO 45001 Occupational Health & Safety & Internal Auditor
Create a safer work environment and reduce workplace incidents. Foster a culture of health and safety, boosting employee morale and productivity. Learn to identify and mitigate occupational health and safety risks. Ensure adherence to global safety standards and avoid costly penalties.
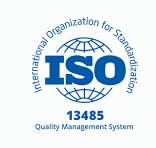
ISO 13485 Medical Device & Internal Auditor
Gained specialized knowledge for the medical device industry. Ensured compliance with global medical device regulations. Develop the ability to conduct internal audits specific to medical devices.
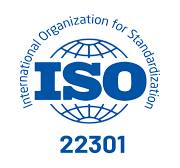
ISO 22301 Business Continuity Management & Internal Auditor
Learn to create robust business continuity plans to withstand disruptions. Identify and manage risks to ensure uninterrupted operations. Develop skills to respond effectively to emergencies and minimize downtime. Demonstrate reliability and build trust with customers and partners.
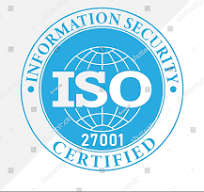
ISO 27001 Information Security Management System
Learn to safeguard sensitive information and prevent data breaches. Gain skills to manage and mitigate information security risks. Ensure alignment with global data protection laws and standards. Build confidence by demonstrating a commitment to information security.
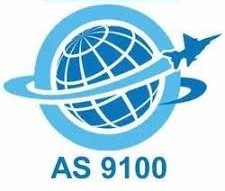
AS 9100 Aerospace Management System & Internal Auditor
Gain specialized knowledge for aerospace quality management. Ensure compliance with aerospace standards and improve supplier relationships. Learn to identify and mitigate risks in aerospace operations. Develop the ability to conduct internal audits specific to the aerospace sector.
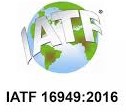
IATF 16949 Automotive Management System & Internal Auditor
Gain expertise in automotive quality management. Learn to improve efficiency and reduce defects in automotive manufacturing. Meet the high-quality expectations of automotive customers. Develop the ability to conduct internal audits specific to the automotive sector.
Quality Tools Training Courses
Comprehensive training on Quality Tools Techiques.
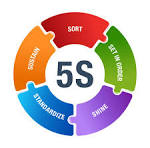
5S Methodology
Implementing 5S results in cleaner, more organized workspaces, leading to improved efficiency and productivity. 5S encourages a culture of ongoing refinement and operational excellence, allowing businesses to remain competitive.
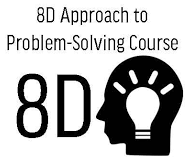
8 Disciplines Problem Solving Process (8D)
The 8D methodology provides a structured framework for addressing complex issues, leading to more effective solutions. It ensures that problems are analyzed deeply to uncover the true cause, preventing recurring issues. The process encourages teamwork across departments, leveraging diverse expertise for holistic solutions.
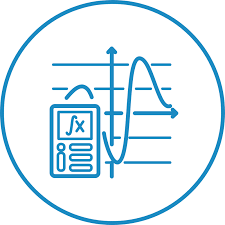
Statistical Process Control (SPC)
SPC empowers employees to make decisions based on real-time data, enhancing control over processes. By monitoring process variation, SPC helps in detecting problems early, reducing downtime and waste. It ensures that processes operate within set limits, enhancing product quality and reducing variability.
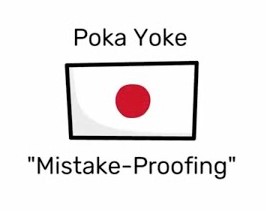
Mistake Proofing (Poka-Yoke)
Poka-Yoke focuses on designing processes that prevent mistakes from occurring, improving product quality and reducing rework. By preventing defects and mistakes, customer complaints and returns decrease, leading to higher satisfaction and loyalty. Preventing mistakes from happening upfront reduces costly repairs, rework, and waste. It simplifies tasks for workers, as the system is designed to minimize errors and make processes foolproof.
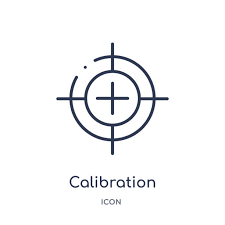
Calibration System
A robust calibration system ensures that instruments and tools provide accurate and reliable measurements, critical for product quality. Regular calibration ensures compliance with industry standards and regulations, preventing costly fines and product recalls. Accurate measurements lead to more consistent and reliable production processes, reducing variation and defects.
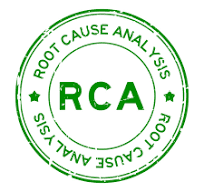
Root Cause Analysis (RCA)
RCA helps identify and address the underlying causes of issues, leading to long-term fixes rather than temporary solutions. By practicing RCA, teams develop critical thinking and analytical skills, improving their ability to solve problems effectively. By addressing real root causes, businesses can reduce operational disruptions, rework, and warranty claims.

Sampling Plan Methodology
Sampling plans allow companies to evaluate product quality without inspecting every single unit, saving time and money. By using well-defined sampling methods, businesses can ensure that results are statistically valid and reliable. With proper sampling, risks associated with defective products are identified early, minimizing potential losses.
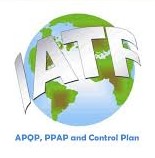
APQP & PPAP
APQP provides a structured approach for developing products that meet customer expectations from the outset. The APQP and PPAP processes help identify potential risks early in the development stage, reducing the likelihood of defects during production. With clear guidelines for quality assurance, suppliers are better equipped to meet quality expectations, fostering stronger collaboration.
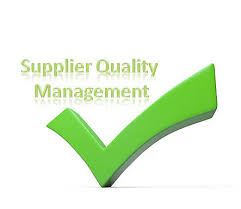
Supplier Quality Management
By working closely with suppliers to improve quality standards, businesses can build stronger, more collaborative partnerships. Supplier quality management ensures that suppliers meet the expected standards, leading to fewer defects and higher-quality materials or components. By ensuring that suppliers deliver quality goods on time and within specifications, businesses can avoid costly disruptions and rework.
Customized Training Courses Tailored to Your Organization
We offer customized training programs designed specifically for your organization’s needs and challenges.
- Industry-specific case studies and examples
- Focus on your organization’s specific quality challenges
- Flexible scheduling to accommodate your team’s availability
- On-site training options available
- Post-training support and implementation guidance
Beyond Training – Consulting Service
We offer consulting services to help you implement what you have learned.
- Quality Management System Implementation
- Process Improvement Projects
- Audit Preparation
- Quality Tools Implementation
- Digitalization of the Quality Management
Ready to Enhance Your Skills ?
Contact us today to discuss your training needs or enroll for an upcoming course.